راکتورها در تولید انواع رزینها نقش مهمی دارند. رزینها مواد پلیمری هستند که به صورت گسترده در صنایع مختلف مانند صنایع پلاستیک، رنگ و رزین، رزینهای کامپوزیت، صنایع ساختمانی و غیره استفاده میشوند. راکتورها در فرآیندهای تولید و سنتز این رزینها نقش اساسی را ایفا میکنند.
برای تولید رزینها، مواد اولیه شیمیایی مختلفی مانند مونومرها و روغنها به واکنش در میآیند. در این فرآیندها، راکتورها به عنوان محیطی برای انجام واکنشها مورد استفاده قرار میگیرند. طراحی راکتور بر اساس نوع واکنش و مشخصات فیزیکوشیمیایی مواد اولیه انجام میشود. یکی از مثالهای رایج راکتورها در تولید رزینها، راکتور پلیمریزاسیون است. در این نوع راکتور، مونومرها تحت واکنش پلیمریزاسیون قرار میگیرند و به صورت یک زنجیره پلیمری طولانی ترکیب میشوند. راکتورهای پلیمریزاسیون معمولاً شامل یک راکتور باز واکنش، سیستم تغذیه مونومرها و همچنین سیستم خنککننده برای کنترل دما هستند.
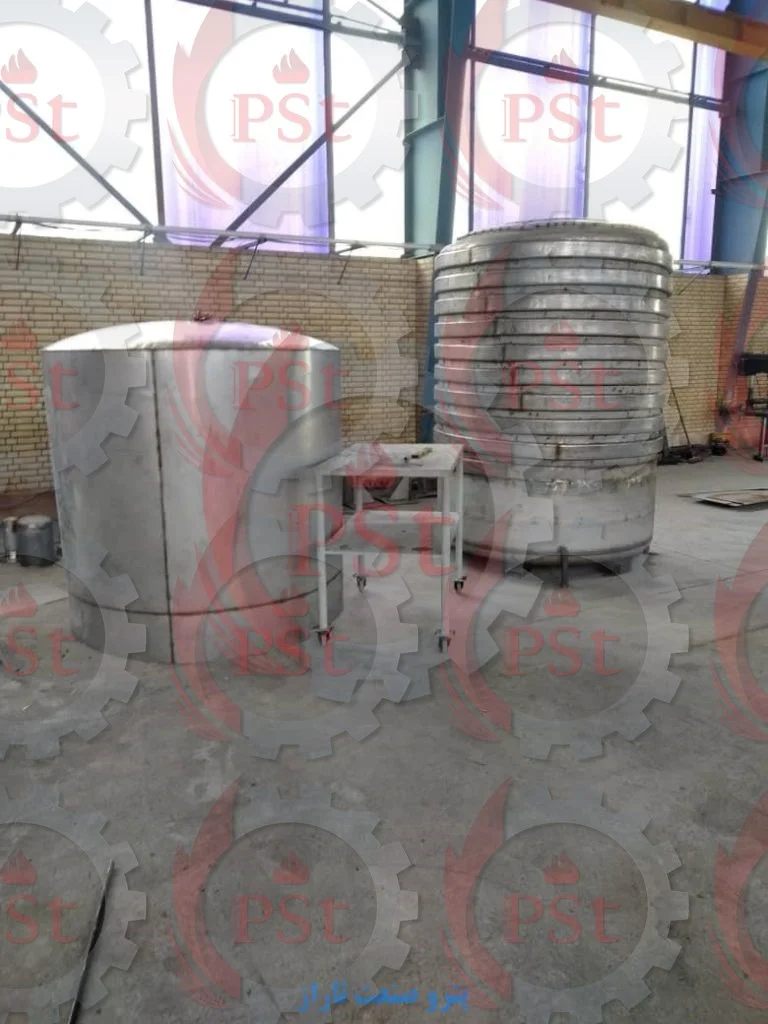
علاوه بر راکتورهای پلیمریزاسیون، راکتورهای دیگری نیز در تولید رزینها استفاده میشوند مانند راکتورهای استریفیکاسیون، راکتورهای کراکینگ و راکتورهای پلیاستریفیکاسیون. هر کدام از این راکتورها بر اساس نوع واکنش و روش تولید رزین مورد استفاده قرار میگیرند. استفاده از راکتورها در تولید رزینها امکان تنظیم و کنترل ویژگیهای فیزیکی و شیمیایی رزینها را فراهم میکند. همچنین، با استفاده از راکتورها میتوان بهبود عملکرد فرآیندهای تولید، افزایش بهرهوری و کاهش هزینهها را دستیابی کرد.
رزین چیست؟
رزینها موادی هستند که در واقع از اتصال تعداد زیادی واحد مولکولی به یکدیگر تشکیل میشوند و به طور کلی به موادی اطلاق میشود که به صورت طبیعی یا مصنوعی وجود دارند و در حالت غیرمذاب سفت و الاستیک هستند. رزینها معمولاً به صورت جامد بوده و میتوانند در حالت طبیعی از گیاهان، حشرات، صدفها، سنگها و دیگر منابع استخراج شوند، یا به صورت مصنوعی تولید شوند. رزینها در صنایع مختلف و بسیاری از محصولات استفاده میشوند. برخی از کاربردهای رزینها عبارتند از:
- صنایع رنگ و رزین: رزینها برای تولید رنگها، رزینهای صنعتی، رزینهای آغشته به مواد رنگزا و پوششهای محافظ استفاده میشوند.
- صنایع چوب و مبلمان: رزینها در تولید چوبچندلایه، تختههای فیبری، مادربورد و مصنوعات چوبی کاربرد دارند. همچنین، در تولید محصولات مبلمان و پوششهای چوبی استفاده میشوند.
- صنعت الکترونیک: رزینها در تولید مواد نیمهرساناها، عایقها، عناصر الکترونیکی و بردهای مدار چاپی استفاده میشوند.
- صنعت خودروسازی: رزینها در تولید قطعات خودرو مانند بدنه، روکش داخلی، لنت ترمز و غیره استفاده میشوند.
- صنایع ساختمانی: رزینها در تولید مواد عایق حرارتی و صوتی، چسبها، روکشهای ضدآب و مواد مقاوم در برابر آتش استفاده میشوند.
- صنایع غذایی: برخی رزینها در تهیه مواد غذایی مانند شیرینیپزی، آدامس و شوکولات استفاده میشوند.
- صنایع دارویی: رزینها در تولید داروها، عصارهها، پوششهای دارویی و کپسولها مورد استفاده قرار میگیرند.
- صنایع آرایشی و بهداشتی: رزینها در تولید لاکها، مواد ثابت کننده، ماسکها، صابونها و محصولات آرایشی استفاده میشوند.
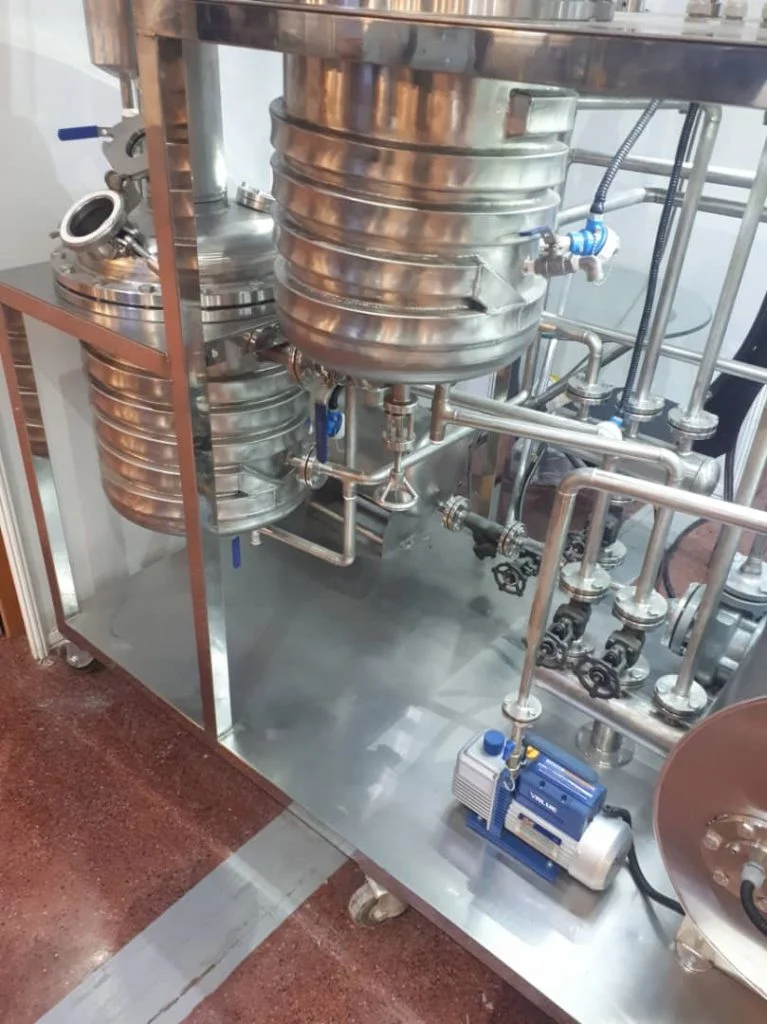
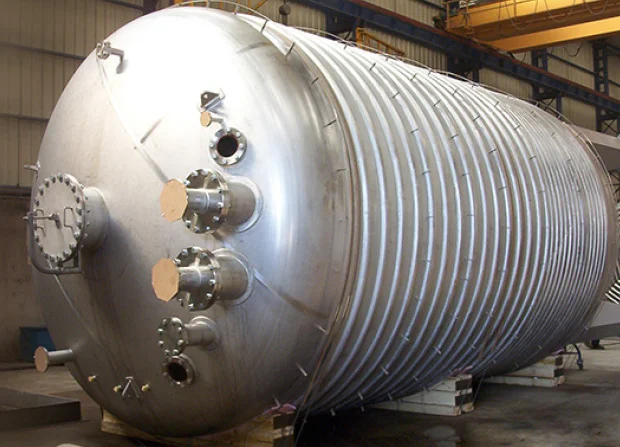
این موارد فوق تنها نمونههایی از کاربردهای رزینها هستند و در واقع رزینها در بسیاری از صنایع و محصولات مختلف به عنوان ماده اصلی یا ماده افزودنی استفاده میشوند. ترکیبات رزینی در عمل به دلیل خواص انعطافپذیری، مقاومت، الاستیسیته، عایقبندی و زیبایی مورد توجه قرار میگیرند و برای انواع محصولات مهمی مانند پوششها، عایقها، چسبها، لاستیکها، فرمولاسیونهای دارویی و غیره به کار میروند.
تولید رزین
تولید رزینها ممکن است به دو روش اصلی انجام شود: روشهای طبیعی و روشهای مصنوعی.
- روشهای طبیعی:
روشهای طبیعی شامل استخراج رزین از منابع طبیعی مانند درختان، گیاهان، صدفها و حشرات است. در این روش، رزین از منابع طبیعی به صورت مایع یا جامد استخراج میشود. فرآیند استخراج ممکن است شامل مراحلی مانند برداشت، برش، سوراخکاری و یا موارد دیگر باشد. سپس رزین استخراج شده تمیز میشود و به صورت مایع یا جامد برای استفاده در صنایع مختلف آماده میشود. - روشهای مصنوعی:
روشهای مصنوعی شامل فرآیندهای شیمیایی و صنعتی برای تولید رزینها هستند. این روشها در اکثر موارد از مواد اولیه پتروشیمیایی مانند هیدروکربنها استفاده میکنند. یکی از فرایندهای معمول برای تولید رزین مصنوعی، پلیمریزاسیون است. در این فرآیند، واکنشهای شیمیایی بین مونومرها با استفاده از محفظهها و فرآیندهای خاصی صورت میگیرد تا رزینهای پلیمری تولید شوند. سپس رزینهای تولید شده تمیز میشوند و ممکن است از طریق فرآیندهای دیگر مانند اصلاح حرارتی، اصلاح شیمیایی و یا تهیه فراوردههای رزینی دیگر بهبود یابند.
در هر دو روش طبیعی و مصنوعی، مراحل پالایش و تصفیه نهایی برای حذف آلودگیها و بهبود کیفیت رزینها نیز انجام میشود. این مراحل شامل تصفیه مکانیکی، استفاده از حلالها، استفاده از فیلتراسیون و جذب مواد ناخالصی است. مقدار و نوع روش تولید رزینها بستگی به نوع رزین و کاربردهای نهایی آن دارد. همچنین، فرآیندهای تولید رزینها ممکن است بر اساس فناوریها و تکنیکهای پیشرفتهتری که در صنایع شیمیایی و پلیمری استفاده میشود، تغییر کند.
راکتورها در فرآیند تولید رزین نقش مهمی ایفا میکنند. راکتورها محیطهایی هستند که در آن واکنشهای شیمیایی برای تبدیل مواد اولیه به رزین انجام میشود. نقش اصلی راکتورها در فرآیند تولید رزین عبارتند از:
- ایجاد شرایط واکنش مناسب: راکتورها شرایطی را فراهم میکنند که واکنشهای شیمیایی مورد نیاز برای تشکیل رزین در آن انجام شود. این شرایط میتواند شامل دما، فشار، زمان و محیطهای حاکم بر واکنش باشد. با اعمال شرایط مناسب در راکتور، میزان و کیفیت تشکیل شده رزین قابل کنترل خواهد بود.
- تبدیل مواد اولیه به رزین: در راکتورها، واکنشهای شیمیایی اصلی برای تبدیل مواد اولیه (مانند مونومرها) به رزین صورت میگیرد. این واکنشها ممکن است شامل پلیمریزاسیون، کوپلینگ یا ترکیب مولکولی دیگر باشد. راکتورها با ارائه شرایط مناسب برای این واکنشها، به تشکیل رزین با خواص و ساختار مورد نظر کمک میکنند.
- کنترل پارامترهای فرآیند: راکتورها امکان کنترل دما، فشار و سایر پارامترهای مرتبط با فرآیند تولید رزین را فراهم میکنند. این کنترلها به دستگاههای حرارتی و ابزارهای کنترلی مانند سنسورها و کنترلرها متصل میشوند. با کنترل دقیق این پارامترها، میتوان به دستیابی به خواص و کیفیت مطلوب رزین نهایی کمک کرد.
- افزایش بهرهوری و کارایی: استفاده از راکتورها به افزایش بهرهوری و کارایی فرآیند تولید رزین کمک میکند. با استفاده از راکتورهای مناسب، میزان تبدیل مواد اولیه به رزین به حداکثر میرسد و ضایعات کاهش مییابد. همچنین، راکتورها میتوانند به کاهش زمان واکنش و افزایش سرعت تولید رزین کمک کنند.
به طور خلاصه، راکتورها در فرآیند تولید رزین نقش کلیدی دارند. آنها شرایط محیطی را فراهم میکنند که واکنشهای شیمیایی برای تبدیل مواد اولیه به رزین صورت گیرد. همچنین، با کنترل پارامترهای فرآیند و بهبود بهرهوری، کیفیت و میزان تولید رزین را بهبود میبخشند.
خط تولید رزین
خط تولید رزین ممکن است شامل چندین تجهیزات و واحد مختلف باشد، که هر کدام وظایف خاص خود را در فرآیند تولید دارند. در زیر تجهیزاتی که معمولاً در یک خط تولید رزین استفاده میشوند را برای شما لیست کردهام:
- واحد مواد اولیه: در این واحد، مواد اولیه برای تولید رزین، مانند مونومرها، پلیمرها، حلالها و مواد شیمیایی دیگر، ذخیره و آماده سازی میشوند.
- واحد پیشتیمار: در این واحد، مواد اولیه پالایش میشوند و فرایندهایی مانند تصفیه، تجزیه، تقطیر و اصلاح شیمیایی بر روی مواد اولیه انجام میشود تا کیفیت و خلوص مواد بهبود یابد.
- واحد پلیمریزاسیون: در این واحد، فرآیندهای پلیمریزاسیون برای تولید رزینهای پلیمری انجام میشود. مونومرها به وجود آمده تحت شرایط واکنشی خاص به هم متصل میشوند و زنجیرههای پلیمری شکل میگیرند.
- واحد فرآیند: در این واحد، مواد رزینی تولید شده از واحد پلیمریزاسیون مورد فرآیندهای دیگری قرار میگیرند. این فرآیندها ممکن است شامل اصلاح حرارتی، تهیه فراوردههای رزینی، تغییر شکل، تمیز کردن و دیگر فرایندهای مکانیکی و شیمیایی باشد.
- واحد بستهبندی: در این واحد، رزینهای تولید شده بستهبندی میشوند. این ممکن است شامل بستهبندی در ظروف مناسب، تزریق به بشکهها یا کیسهها، اعمال برچسب و مارکینگ و دیگر فرآیندهای مربوط به بستهبندی باشد.
علاوه بر اینها، خطوط تولید رزین ممکن است از تجهیزات دیگری مانند مخازن تخزیین، پمپها، سیستمهای خنککننده، سیستمهای گرمایشی، سیستمهای کنترل و نظارت و دستگاههای انتقال مواد (مانند نوار نقاله و سیستمهای خمیری) استفاده میکنند. مقیاس و پیچیدگی خط تولید رزین ممکن است بسته به نوع رزین و ظرفیتتولید رزین ممکن است به روشهای مختلف انجام شود، اما در کل عملیات تولید رزین شامل مراحل زیر است:
- مواد اولیه: در ابتدا، مواد اولیه مورد نیاز برای تولید رزین جمع آوری میشوند. این مواد میتوانند شامل مواد شیمیایی، ترکیبات طبیعی، منابع نفتی و غیره باشند.
- فرآیند تهیه مواد اولیه: مرحله بعدی شامل فرآیندهایی است که مواد اولیه را برای استفاده در تولید رزین آماده میکند. این مرحله ممکن است شامل تصفیه، تجزیه، تقطیر و مراحل دیگر باشد.
- رآکتور: مواد اولیه آماده شده به رآکتور منتقل میشوند. در رآکتور، واکنشهای شیمیایی انجام میشود تا مواد اولیه به رزین تبدیل شوند. شرایط دما، فشار و زمان در این مرحله کنترل میشوند تا واکنش به درستی اتفاق بیافتد.
- فرآیندهای پساواکنش: پس از اتمام واکنش در رآکتور، رزین تولید شده در فرآیندهای پساواکنش قرار میگیرد. این فرآیندها ممکن است شامل تصفیه، تنظیم خواص فیزیکی و شیمیایی، تغییر شکل و دیگر عملیات باشد.
- بستهبندی و ذخیره سازی: در این مرحله، رزین تولید شده بستهبندی میشود. رزین در ظروف مناسب قرار میگیرد و ممکن است برای ذخیره سازی و حمل و نقل به انبارها یا بازارها منتقل شود.
به علاوه، خط تولید رزین ممکن است شامل تجهیزاتی مانند مخازن، میکسرها، رآکتورها، سیستمهای تغذیه، سیستمهای خنککننده، سیستمهای کنترل و نظارت، تجهیزات بستهبندی و دستگاههای انتقال مواد (مانند نوار نقاله و پمپها) باشد. لازم به ذکر است که دقیقاً چه تجهیزاتی در یک خط تولید رزین استفاده میشود، بستگی به اندازه و نوع تولید، فناوری مورد استفاده و سیستم تولید خاصی که شرکت یا کارخانه اجرا میکند، دارد.
خط تولید رزین به صورت کلی شامل مجموعهای از تجهیزات و دستگاههای مختلف است که برای تولید رزین به کار میروند. البته، تجهیزات مورد استفاده وابسته به نوع و فرآیند تولید رزین است و ممکن است با تفاوتهایی روبرو شود. در ادامه، تعدادی از تجهیزات معمولاً در خط تولید رزین ذکر میشوند:
مخازن و مخازن مخلوط کننده: برای مخلوط کردن و آماده سازی مواد اولیه و مواد شیمیایی مورد نیاز در فرآیند تولید رزین استفاده میشود. این مخازن معمولاً دارای سیستمهای تغذیه و تخلیه مواد نیز هستند.
- تجهیزات انتقال مواد: شامل لولهها، پمپها و سیستمهای انتقال فشار میشود که برای انتقال مواد از مخازن به سایر بخشهای خط تولید مورد استفاده قرار میگیرد.
- راکتورها: راکتورها برای انجام واکنشهای شیمیایی و پلیمریزاسیون مورد استفاده قرار میگیرند. این راکتورها میتوانند مخازن تحت فشار، سیستمهای ترمواستات، راکتورهای پلیمری و غیره باشند.
- سیستمهای حرارتی: برای تأمین و کنترل دما در فرآیندهای حرارتی مانند تهیه رزینها، روشهای اصلاح حرارتی و یا تصفیه رزینها استفاده میشود. این سیستمها ممکن است شامل چیلرها، بویلرها، حرارتدهندهها و یا سیستمهای خنک کننده باشند.
- دستگاههای خنک کننده و جامدسازی: بعد از فعالیتهای شیمیایی و پلیمریزاسیون، رزین ممکن است نیاز به خنک شدن و جامدسازی داشته باشد. برای این منظور، دستگاههای خنک کننده، آبگرمکن و یا تجهیزاتی برای جذب حرارت مورد استفاده قرار میگیرند.
- واحدهای فرآوری و پالایش: برای تصفیه و پالایش رزینها و حذف آلودگیها و ناخالصیها، واحدهایی مانند فیلتراسیون، جذب، تقطیر و تصفیه ممکن است در خط تولید مورد استفاده قرار گیرند.
- سیستمتجهیزات انتقال و بستهبندی: برای انتقال رزین تولید شده به محصول نهایی و بستهبندی آن، از تجهیزاتی مانند پمپها، لولهها، تانکرها، دستگاههای بستهبندی و برچسبزنی استفاده میشود.
موارد فوق تنها برخی از تجهیزات معمولاً در خط تولید رزین هستند و بسته به نوع رزین و فرآیند تولید، ممکن است تجهیزات دیگری نیز در خط تولید مورد استفاده قرار گیرند. همچنین، خط تولید ممکن است شامل کنترلها و سیستمهای اتوماسیون برای کنترل و نظارت بر فرآیند تولید باشد.
فرآیند تولید رزین
فرآیند تولید رزین میتواند با توجه به نوع رزین و مصارف مختلف آن، متفاوت باشد. در ادامه، یک نمونه از فرآیند تولید رزین را بررسی میکنیم:
مواد اولیه: مواد اولیه مورد استفاده در تولید رزین میتوانند شامل مواد پلیمری، مواد شیمیایی و مواد افزودنی دیگر باشند. مثالهایی از مواد اولیه شامل مونومرها (مانند استایرن)، مواد افزودنی (مانند ماده پرکننده و آنتیاکسیدان) و محلولهای حلال میشود.
- مخلوط کردن: در این مرحله، مواد اولیه به مخازن مخلوط کننده منتقل میشوند. در این مخازن، مواد اولیه با استفاده از پمپها و سیستمهای انتقال مواد مخلوط میشوند. این مرحله ممکن است شامل تنظیم دما، فشار و سایر شرایط فرآیند باشد.
- واکنش شیمیایی: در این مرحله، مواد اولیه مخلوط شده به راکتورها منتقل میشوند. در راکتورها، واکنشهای شیمیایی مانند پلیمریزاسیون رخ میدهند. با اعمال شرایط مناسب، مونومرها به زنجیرههای بلندتر تبدیل میشوند و رزین شکل میگیرد.
- کنترل دما و زمان: در این مرحله، دما و زمان واکنش تحت کنترل قرار میگیرند. این کنترلها به دستگاههای حرارتی مانند چیلرها، بویلرها و حرارتدهندهها اعمال میشود. هدف از این مرحله، دستیابی به ویژگیهای مطلوب رزین نهایی است.
- خنک کردن و جامدسازی: پس از اتمام واکنش، رزین در مرحله جامدسازی قرار میگیرد. این مرحله شامل خنک کردن رزین تا دمای مورد نیاز و استفاده از دستگاههای خنک کننده و جامدسازی میشود. در نهایت، رزین به شکل جامد خروجی داده میشود.
- تصفیه و پالایش: رزین جامد تولید شده ممکن است ناخالصیها و آلودگیهایی داشته باشد. در این مرحله، از فیلتراسیون، جذب و تصفیهگرهای دیگر برای حذف ناخالصیها و بهبود کیفیت رزین استفاده میشود. این فرآیند تصفیه و پالایش باعث افزایش خلوص و استحکام رزین میشود.
- بستهبندی و توزیع: پس از تصفیه و پالایش، رزین جامد به مرحله بستهبندی و آمادهسازی برای توزیع میرسد. در این مرحله، رزین به طریقهای مناسب بستهبندی میشود تا در حمل و نقل و ذخیرهسازی از آسیب جلوگیری شود.
مراحل بالا تنها مراحل عمومی فرآیند تولید رزین را شرح دادهاند. در عمل، فرآیند تولید رزین ممکن است شامل مراحل بیشتر و تجهیزات واحد دیگری نیز باشد که بسته به نوع رزین و نیازهای خاص تولید کننده متفاوت خواهد بود. همچنین، استفاده از فناوریهای پیشرفته و کنترلهای دقیق در فرآیند تولید رزین میتواند به بهبود کیفیت و کارایی فرآیند کمک کند.
ساخت راکتور تولید رزین
راکتورهای استفاده شده در تولید رزین ممکن است متنوع باشند و بسته به نوع رزین و فرآیند تولید مورد استفاده، استانداردها، متریالها و روشهای ساخت آنها متفاوت خواهد بود. در ادامه، به برخی از انواع راکتورها و ویژگیهای آنها اشاره میکنم:
- راکتورهای پلیمریزاسیون: برای تولید رزینهای پلیمری، راکتورهای پلیمریزاسیون استفاده میشود. این راکتورها معمولاً از جنس استیل یا فولاد ضدزنگ تولید میشوند که مقاومتی در برابر شیمیاییها و حرارت داشته باشند. استانداردهای مرتبط با راکتورهای پلیمریزاسیون میتواند شامل استانداردهای ASTM D3299 و ASME Boiler and Pressure Vessel Code باشد.
- راکتورهای ترکیب مولکولی: در فرآیندهای تولید رزینهای ترکیبی، راکتورهای ترکیب مولکولی ممکن است استفاده شوند. این راکتورها ممکن است از متریالهای مختلفی مانند استیل، فولاد ضدزنگ، آلومینیوم یا مواد پلیمری ساخته شوند. استانداردهای مرتبط با راکتورهای ترکیب مولکولی میتواند شامل استانداردهای ASTM D4702 و API 660 باشد.
- راکتورهای ترموسِتینگ: در فرآیندهای تولید رزینهای ترموستینگ، راکتورهای ترموسِتینگ برای اجرای واکنشهای شیمیایی در دماهای بالا استفاده میشوند. این راکتورها معمولاً از متریالهای مقاوم در برابر حرارت و فشار مانند فولاد ضدزنگ یا آلیاژهای خاص تولید میشوند. استانداردهای مرتبط با راکتورهای ترموسِتینگ ممکن است شامل استانداردهای ASME Boiler and Pressure Vessel Code و API RP 552 باشد.
لازم به ذکر است که در عمل، ساخت راکتورها بسته به نیازهای خاص فرآیند تولید و تکنولوژی مورد استفاده متفاوت خواهد بود. برای اطمینان از استفاده از راکتورهای مناسب و رعایت استانداردهای لازم، مشاوره با مهندسان و کارشناسان مجرب شرکت پترو صنعت تاراز توصیه میشود.
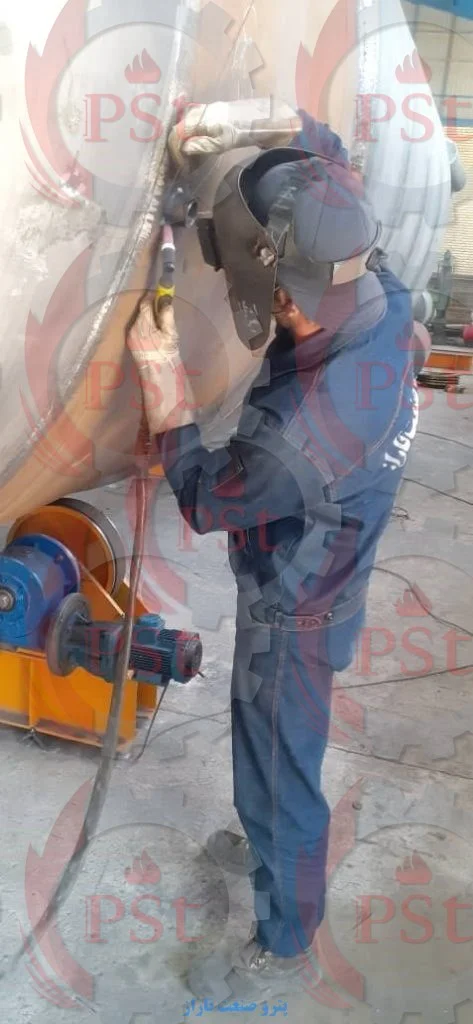
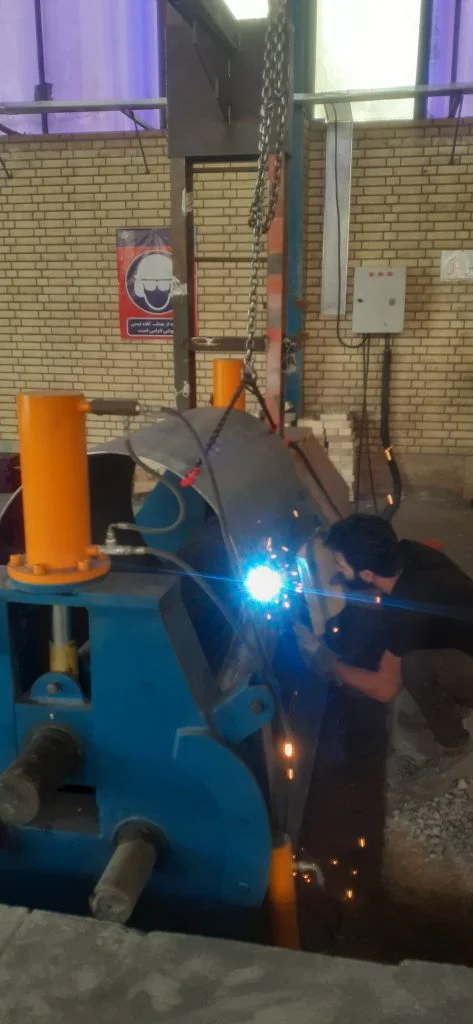
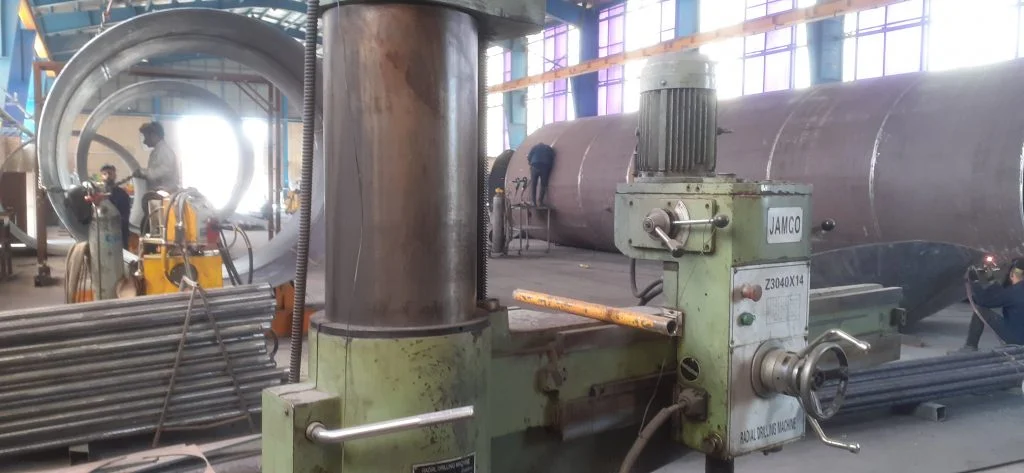
راکتورهای استفاده شده در صنعت رزینسازی معمولاً از جنسهای استیل (مانند فولاد ضدزنگ) و یا آلیاژهای خاص ساخته میشوند. استیل به علت مقاومت بالا در برابر خوردگی شیمیایی و حرارت، محبوبیت بالایی برای ساخت راکتورها در صنایع شیمیایی دارد. در موارد خاص، ممکن است از مواد دیگری مانند آلومینیوم یا مواد پلیمری نیز برای ساخت بدنه راکتور استفاده شود.
بدنه راکتورها عموماً از ورقهای فلزی ساخته میشوند که با استفاده از روشهای جوشکاری متنوع به یکدیگر متصل میشوند. نوع جوشکاری که در ساخت راکتورها استفاده میشود، بسته به نوع متریال و نیازهای فرآیند ممکن است متفاوت باشد. برخی از روشهای جوشکاری معمول شامل موارد زیر است:
- جوشکاری تیغه: در این روش، تیغههای فلزی بر روی یکدیگر قرار داده شده و با استفاده از جوشکاری پلتین بین آنها جوش داده میشوند. این روش معمولاً برای اتصال ورقهای تخت و مسطح استفاده میشود.
- جوشکاری توپی: در این روش، دو قسمت منحنی یا کروی به هم متصل میشوند. جوشکاری توپی میتواند به صورت جوشکاری توپی تکمیلی (Full-Penetration Welding) یا جوشکاری توپی نیمه تکمیلی (Partial-Penetration Welding) انجام شود.
- جوشکاری مخزنی: در راکتورهای با حجم بزرگتر، ممکن است از جوشکاری مخزنی استفاده شود. در این روش، بخشهای مخزن را با هم جوش میدهند تا یک بدنه محکم و بدون اتصالات غیرضروری ایجاد شود.
لازم به ذکر است که نوع جوشکاری و متریال مورد استفاده در ساخت راکتورها باید با استانداردها و مقررات مربوطه (مانند استانداردهای ASME) سازگار باشد تا اطمینان از استحکام و ایمنی راکتور به دست آید. همچنین، برای طراحی و ساخت راکتورها، مهندسان و کارشناسان مجرب در زمینه صنعت رزینسازی معمولاً درگیر هبا عرض پوزش، به نظر میرسد برخی از جزئیات پاسخ قبلی از بین رفته باشد. در مورد جنس بدنه و نوع جوشکاری راکتور رزینسازی، میتوانم اطلاعات بیشتری ارائه دهم:
جنس بدنه راکتورها در صنعت رزینسازی معمولاً از جنس استیل ضدزنگ مانند استیل آستنیتیک (مانند 316 و 304) یا آلیاژهایی مانند Duplex و Super Duplex ساخته میشود. استیل ضدزنگ به دلیل مقاومت بالا در برابر خوردگی شیمیایی و حرارت، محبوبیت بالایی برای ساخت راکتورهای صنعتی دارد. استفاده از آلیاژهای خاص نیز برای افزایش مقاومت در برابر خوردگی و خستگی میتواند مورد استفاده قرار گیرد.
نوع جوشکاری که در ساخت راکتورهای صنعتی استفاده میشود، معمولاً به استانداردهای مربوطه مانند ASME Boiler and Pressure Vessel Code و AWS D1.1 مطابقت دارد. انواع جوشکاری ممکن است شامل موارد زیر باشد:
- جوشکاری TIG (Tungsten Inert Gas Welding): در این روش، یک الکترود تنگستن غیرفلزی با استفاده از یک گاز حفاظتی برای جوشکاری در محلول جوشکاری استفاده میشود.
- جوشکاری MIG (Metal Inert Gas Welding): در این روش، الکترود فلزی به عنوان منبع جوش استفاده میشود و گاز حفاظتی برای جلوگیری از تماس جوش با هوا مورد استفاده قرار میگیرد.
- جوشکاری SMAW (Shielded Metal Arc Welding): در این روش، الکترود مصرفی فلزی با پوشش محافظ استفاده میشود و قوس الکتریکی بین الکترود و قطعه کار ایجاد میشود.
- جوشکاری SAW (Submerged Arc Welding): در این روش، قوس الکتریکی بین یک الکترود فلزی و قطعه کار در محلول جوش به وجود آمده و با پوشش یک لایه محافظ، جوشکاری انجام میشود.
نوع جوشکاری مورد استفاده بستگی به نوع متریال، ضخامت بدنه راکتور و نیازهای فنی دارد. با این حال، برای دقت و تأیید اطلاعات، بهتر است با مهندسان و کارشناسان مجرب در زمینه ساخت راکتورهای صنعتی شرکت پترو صنعت تاراز تماس بگیرید.