راکتور تولید رزین اپوکسی یک واحد صنعتی است که برای تولید رزین اپوکسی استفاده میشود. رزین اپوکسی یک نوع رزین ترموستاتیک است که بر اساس ترکیبات اپوکسی و عامل تصلب کننده تشکیل میشود. این رزینها دارای خواص فیزیکی و مکانیکی بسیار عالی هستند و به طور گسترده در صنایع مختلف مانند صنایع پوششدهی، الکترونیک، خودروسازی، ساخت و ساز و غیره استفاده میشوند.
این راکتورها عمدتاً شامل یک سیستم تولید واکنشی است که در آن مواد اولیه مورد نیاز برای تولید رزین اپوکسی به هم مخلوط میشوند و واکنش شیمیایی بین آنها رخ میدهد. این واکنش معمولاً شامل ترکیبات اپوکسی (مانند اپوکسی رزین) و عامل تصلب کننده (مانند آمینها) است که توسط کاتالیزورها و شرایط خاصی همچون دما و فشار، به وقوع میپیوندد.
این دستگاه ها از نظر طراحی و اندازه بندی متنوع هستند. ظرفیت آنها ممکن است از واحدهای کوچک آزمایشگاهی تا واحدهای بزرگ صنعتی متفاوت باشد. در هر صورت، این راکتورها باید توانایی تهیه و مخلوط کردن مواد اولیه، کنترل دما و فشار و فراهم کردن شرایط بهینه برای واکنش شیمیایی را داشته باشند.
رزین اپوکسی چیست؟
رزین اپوکسی یک نوع پلیمر است که از واکنش بین اپوکسیدها (مانند بیسفنول-A اپوکسی) و عوامل تصلب کننده (مانند اتیلن دیآمین) به دست میآید. این واکنش شیمیایی میان گروههای اپوکسیدی و گروههای عامل تصلب کننده، باعث تشکیل لینک های صلب و سه بعدی در ساختار رزین میشود.
رزین اپوکسی دارای خواص مکانیکی بالا، مقاومت شیمیایی، عایق بودن و قابلیت ترکیب با مواد مختلف است. به دلیل این ویژگیها، رزین اپوکسی در صنایع مختلفی مانند صنایع پوششدهی، صنایع الکترونیک، کامپوزیتها، آدزیوها، چسبها و موارد دیگر استفاده میشود.
رزین اپوکسی نوعی پلیمر دو جزئی است که عموماً به صورت مایع یا زلال در دسترس است. این ماده به خاطر خواص برجسته مکانیکی، اثرات الکتریکی، مقاومت در برابر حلال ها، مقاومت در برابر خوردگی و دارا بودن عمر طولانی، از محبوبیت بالایی برخوردار است. رزین اپوکسی در بسیاری از صنایع مانند چسب سازی، بسته بندی، اتومبیل سازی، صنعت الکترونیک و صنعت هوا و فضا استفاده می شود.
خط تولید رزین اپوکسی
راکتور صنعتی برای تولید تجاری رزین اپوکسی به عنوان یک نوع پلیمر، معمولاً یک واکنشگر با ظرفیت بالا و قابلیت کنترل شرایط فرآیند است که قلب اصلی خط تولید رزین اپوکسی میباشد.
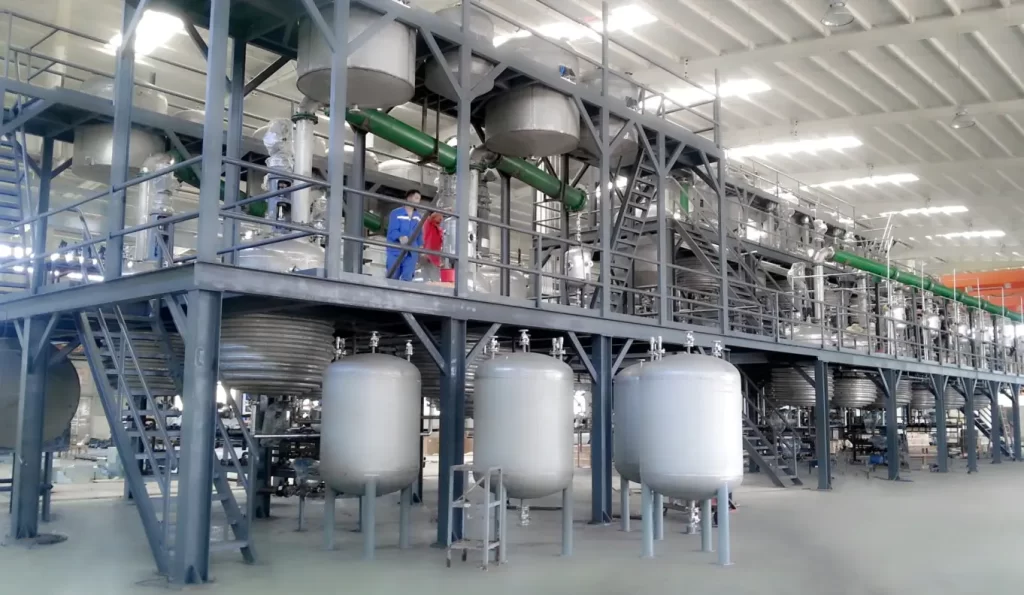
یک کارگاه تولید رزین اپوکسی در مقیاس تجاری و صنعتی ممکن است شامل قسمتها و بخشهای زیر باشد:
- میکسر برای مخلوط کردن مواد اولیه استفاده میشوند. معمولاً دستگاههای مکانیکی مانند میکسرها و مخلوطکنها برای تسهیل مخلوط کردن مواد به کار میروند.
- سیستم تغذیه شامل پمپها و لولهکشی است که برای انتقال مواد از تانکها به راکتور استفاده میشود. پمپها باید قادر به ایجاد فشار و جریان مورد نیاز برای تغذیه مواد به راکتور باشند.
- راکتور تولید رزین اپوکسی قسمت اصلی و مهم تولید است. در این بخش، مواد اولیه (اپوکسی و عامل تصلب کننده) به هم مخلوط میشوند و واکنش شیمیایی بین آنها رخ میدهد. راکتورها معمولاً شامل تجهیزاتی مانند مخلوطکنها، سیستمهای حرارتی (برای کنترل دما) و سیستمهای کاتالیزوری (برای تسریع واکنش) هستند.
- در راکتورهای صنعتی، نیاز به خنککننده برای کنترل دمای راکتور و جلوگیری از افزایش غیرمطلوب دما وجود دارد. این سیستم معمولاً شامل سیستمهای خنککننده آب یا سیال حرارتی میشود.
- پس از اتمام واکنش شیمیایی، محصول تولید شده باید از ترکیبات دیگر جدا شود و تصفیه شود. این بخش شامل تجهیزاتی مانند فیلترها، جداکنندهها و واحدهای تصفیه است.
- یک راکتور تولید رزین اپوکسی باید دارای سیستم کنترل و نظارت مناسب باشد. این سیستم معمولاً شامل سنسورها، حسگرهای دما و فشار، کنترلرها و نمایشگرها است که برای کنترل و نظارت بر عملیات راکتور استفاده میشوند.
راکتور رزین سازی
معمولا برای بدنه راکتور تولید رزین اپوکسی از موادی استفاده میشود که توانایی مقاومت در برابر شیمیایی بودن و تحمل دماهای بالا را داشته باشند. فولادهای ضدزنگ، مانند فولاد ضدزنگ 316 و 304، به علت مقاومت بالا در برابر خوردگی و تحمل دماهای بالا، برای بدنه راکتورهای تولید رزین اپوکسی استفاده میشوند. آلومینیوم به دلیل خواص خود به عنوان یک ماده سبک و مقاوم در برابر خوردگی، در برخی از راکتورهای تولید رزین اپوکسی استفاده میشود. اما باید توجه داشت که آلومینیوم در برخی شرایط شیمیایی خاص ممکن است حساسیت داشته باشد.
راکتور رزین سازی در مقیاس تجاری معمولاً به کندانسور نیاز دارد. در فرآیند تولید رزین اپوکسی، واکنشهای شیمیایی ممکن است باعث تولید گازها و بخاراتی شود که باید از راکتور جدا شوند. برای این منظور، از کندانسور استفاده میشود تا بخارات و گازهای تولید شده را تبدیل به مایع کندانسه کند.
کندانسورها معمولاً شامل یک سیستم خنککننده هستند که بر روی آن گازها و بخارات تصادفی شده و به مایع تبدیل میشوند. این مایع سپس جمعآوری و استفاده مجدد یا دفع میشود. به وسیله کندانسور، میزان بازیابی مواد و کاهش ضایعات ممکن است ممکن شود. توجه داشته باشید که استفاده از کندانسور در راکتورهای تولید رزین اپوکسی معمولاً به دلیل محدودیتهای زیست محیطی و اقتصادی است. با استفاده از کندانسور، میتوان به بهبود بهرهوری، کاهش ضایعات و کنترل آلایندههای محیطی در فرآیند تولید رزین اپوکسی کمک کرد.
در برخی فرآیندهای تولید رزین اپوکسی در مقیاس تجاری، استفاده از وکیوم و خلاء نیز مورد نیاز است. در برخی موارد، مخلوط کردن دقیق رزین اپوکسی با عامل تصلب کننده و دیگر مواد افزودنی ضروری است. استفاده از خلاء در این مرحله میتواند هوا و حبابهای هوا را از مخلوط حذف کند و همچنین به تضمین یکنواختی و کاهش خطر ایجاد حباب در محصول نهایی کمک کند.
در مرحله تصلب رزین اپوکسی، استفاده از وکیوم ممکن است به عنوان روشی برای حذف حبابهای هوا و کاهش ریزشها در نتیجه تصلب مورد استفاده قرار گیرد. با ایجاد فشار کمتر درون راکتور و استفاده از وکیوم، میتوان هوای محبوس درون رزین را از بین برد و به نتیجه بهبوددهی ظاهری و خواص مکانیکی محصول نهایی رسید.
مراحل تولید رزین اپوکسی در راکتور
مواد اولیه در مخازن مخلوطکن به هم مخلوط میشوند. این مخلوطکردن ممکن است به وسیله میکسرها یا دستگاههای مکانیکی دیگر انجام شود تا ترکیبات به طور یکنواخت ترکیب شوند. راکتورها معمولاً شامل مخلوطکنها، سیستمهای حرارتی و سیستمهای کاتالیزوری هستند. در این مرحله، واکنش شیمیایی بین اپوکسی و عامل تصلب کننده آغاز میشود.
در راکتور، واکنش شیمیایی بین اپوکسی و عامل تصلب کننده رخ میدهد. این واکنش شیمیایی عموماً با استفاده از کاتالیزورها، دما و فشار مناسب و زمان مناسب انجام میشود. این واکنش باعث تشکیل لینک های صلب و سلسله مراتبی در ساختار رزین اپوکسی میشود. در طول واکنش شیمیایی، دما و فشار در راکتور کنترل میشوند. دما و فشار مناسب برای واکنش شیمیایی و تشکیل رزین اپوکسی حائز اهمیت است و باید با دقت کنترل شوند.
پس از اتمام واکنش شیمیایی، محصول تولید شده باید از ترکیبات دیگر جدا شود و تصفیه شود. این فرآیند معمولاً شامل استفاده از فیلترها، جداکنندهها، تقطیر، خنککنندهها و واحدهای تصفیه است. پس از جداسازی و تصفیه، ممکن است نیاز به مراحل پسپردازش داشته باشید. این فرآیندها شامل اقداماتی مانند خشک کردن، غلظتدهی، تثبیت رنگ، اضافه کردن مواد افزودنی و سایر مراحل تقویت خواص و کیفیت رزین اپوکسی است.
مواد اولیه مورد نیاز
برای تولید رزین اپوکسی، مواد اولیه اصلی شامل اپوکسید (اپوکسی) و عامل تصلب کننده (معمولاً آمین) است. این دو ماده در ترکیبات مختلف و با نسبتهای متفاوت برای دستیابی به خواص مطلوب رزین اپوکسی استفاده میشوند. اپوکسید یا اپوکسی ماده اصلی و پایه رزین اپوکسی است. اپوکسیدها معمولاً ترکیبات عضوی اپوکسیچین هستند که دو گروه اپوکسیدی (-O-CH2-O-) در ساختار مولکولی خود دارند. مثالهایی از اپوکسیدها عبارتند از: بیسفنول-A اپوکسی (BADGE)، دیگلیسیدیل اتر بیسفنول-A (DGEBA) و نووولاکسید اپوکسی (NHE).
عامل تصلب کننده در واقع عاملی است که با اپوکسید واکنش میدهد و باعث تشکیل لینک های صلب و سلسله مراتبی در ساختار رزین اپوکسی میشود. معمولاً آمین ها به عنوان عامل تصلب کننده در رزین اپوکسی استفاده میشوند. برخی از آمینهای معمول شامل اتیلن دیآمین (EDA)، دیتریآمین (DTA)، دیآمینوفنیل متان (DAPM) و آمینهای آروماتیک هستند.
نسبت مورد استفاده بین اپوکسید و عامل تصلب کننده در تولید رزین اپوکسی ممکن است بسته به نوع و کاربرد مورد نظر متفاوت باشد. در بیشتر موارد، نسبت معمول بین اپوکسید و عامل تصلب کننده در حدود 1:1 تا 3:1 است. این به این معنی است که برای هر گروه اپوکسیدی در ساختار اپوکسید، حدوداً یک گروه عامل تصلب کننده استفاده میشود.
در برخی از موارد، برای افزایش سرعت واکنش شیمیایی بین اپوکسید و عامل تصلب کننده، کاتالیزورها نیز مورد استفاده قرار میگیرند. کاتالیزورها میتوانند مونومرهای آمینی، اسیدها، آمینها، آمیناتها و آمیدها باشند. مثالهایی از کاتالیزورها عبارتند از: دیبوتیلتیندیکلرید (DBTDL)، پارا تولوئن سولفونیک اسید (PTSA) و آمینهای ثانویه.
به عنوان مثال، در صورت استفاده از بیسفنول-A اپوکسی (BADGE) به عنوان اپوکسید و اتیلن دیآمین (EDA) به عنوان عامل تصلب کننده، نسبت معمولی که معمولاً استفاده میشود، یک نسبت 1:1 است. یعنی برای هر مولکول بیسفنول-A اپوکسی، یک مولکول اتیلن دیآمین استفاده میشود.
دما و فشار مناسب تولید رزین اپوکسی
در فرآیند تولید رزین اپوکسی، بسته به نوع واکنش و شرایط مورد استفاده، ممکن است نیاز به منبع گرمایی در مخزن واکنش وجود داشته باشد. این وابسته به سرعت واکنش بین اپوکسید و عامل تصلب کننده، دمای مورد نظر و شرایط محیطی است. دمای تولید رزین اپوکسی معمولاً بین 20-80 درجه سلسیوس قرار دارد. دمای مورد نیاز به عوامل ترکیبی مورد استفاده و خواص مورد نظر رزین بستگی دارد. برای بیشتر فرمولاسیونها، دمای بالاتر معمولاً بهتر است چرا که سرعت واکنش بین اپوکسید و عامل تصلب کننده در دماهای بالاتر افزایش مییابد.
در بیشتر موارد، تولید رزین اپوکسی به فشار خاصی نیاز ندارد و در فشار جو آزاد صورت میگیرد. بنابراین، فشار معمولاً تقریباً برابر با فشار جو آزاد (اتمسفریک) است. مدت زمان تولید رزین اپوکسی نیز بستگی به نوع فرمولاسیون و شرایط استفاده دارد. معمولاً، زمان تقریبی برای تولید رزین اپوکسی در حدود 24-48 ساعت است. اما، در صورت استفاده از کاتالیزورها و مواد افزودنی خاص، زمان تولید ممکن است کاهش یابد و فرآیند را سریعتر کند.
دما، فشار و مدت زمان مناسب برای تولید رزین اپوکسی بستگی به نوع و فرمولاسیون مورد استفاده دارد. در برخی موارد، واکنش بین اپوکسید و عامل تصلب کننده به تنهایی به اندازه کافی گرما تولید میکند و نیازی به منبع گرمایی خارجی نیست. اما، در موارد دیگر، بخصوص در فرمولاسیونهایی که سرعت واکنش بین اپوکسید و عامل تصلب کننده در دماهای پایین بسیار کند است، استفاده از منبع گرمایی برای افزایش دما و تسریع واکنش ممکن است لازم باشد.
جهت کسب اطلاعات بیشتر در مورد قیمت دستگاه تولید رزین اپوکسی با شماره 09133753907 (واحد بازرگانی و فروش شرکت پترو صنعت تاراز) تماس بگیرید.