در زمینه کنترل و مدیریت فرایند واکنش شیمیایی در فشارهای بسیار بالا، موضوعاتی مرتبط با شیمی فیزیکی و شیمی سطح میباشد. در این حوزه، تلاش میشود تا فرایندهای شیمیایی در شرایط فشار بسیار بالا، مانند فشارهای برابر با صدها گیگاپاسکال یا حتی تریلیونها پاسکال، کنترل و بهینهسازی شود.
یکی از موضوعات مهم در این زمینه، بررسی و برهمکنش مواد در فشارهای بسیار بالا است. فشارهای بالا میتوانند خواص فیزیکی و شیمیایی مواد را تغییر داده و واکنشهای شیمیایی را به شکلهای جدیدی انجام دهند. بررسی این واکنشها و بهبود شرایط آنها میتواند به منظور بهبود عملکرد فرایندهای صنعتی، تولید مواد جدید و کشف واکنشهای شیمیایی نوین مورد استفاده قرار گیرد.
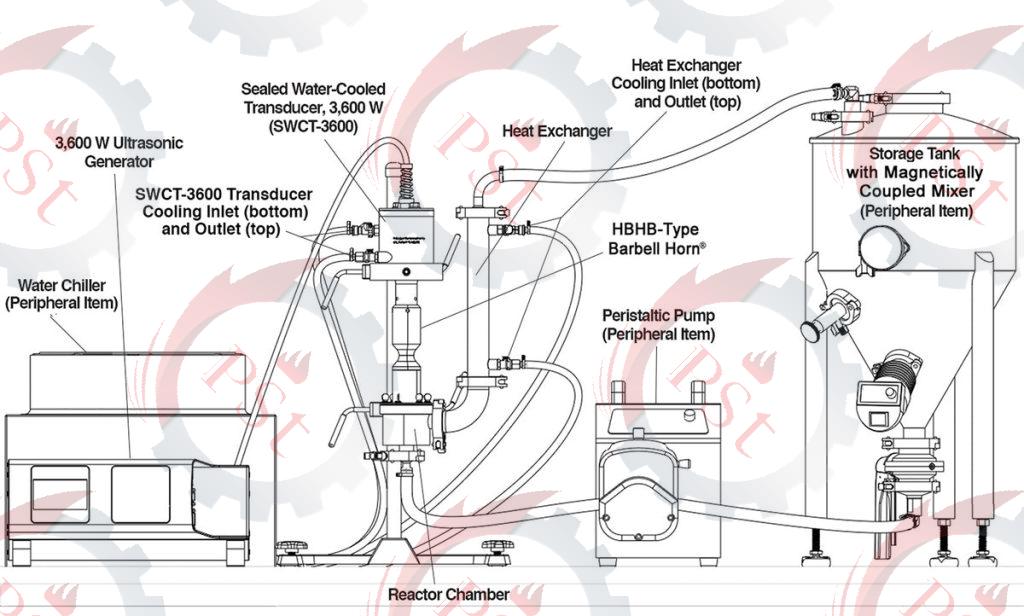
یکی دیگر از مسائل مهم در این حوزه، کنترل فرایندهای شیمیایی در فشارهای بسیار بالا است. فشارهای بالا ممکن است باعث ایجاد شرایط پیچیدهتری در فرایندهای شیمیایی شود و کنترل آنها چالشهایی را ایجاد کند. بررسی روشهای کنترل فرایندها، شناخت پارامترهای مؤثر و توسعه روشهای کنترل پیشرفته میتواند به بهبود کارایی و کیفیت فرایندها کمک کند.
همچنین، در زمینه کنترل و مدیریت فرایند واکنش شیمیایی در فشارهای بالا، بهبود روشهای نمونهبرداری، تجزیه و تحلیل نمونهها و کنترل راکدگی نیز از اهمیت بالایی برخوردار است. در کل، این زمینه تلاش میکند تا با استفاده از دانش شیمی، فیزیک و مهندسی، بهبود فرایندهای شیمیایی در فشارهای بسیار بالا را ممکن سازد و به کاربردهای گستردهتری در صنایع شیمیایی، نیروگاهی، مواد اولیه و سایر صنایع برساند.
چالش های واکنش شیمیایی در فشار بسیار بالا
واکنشهای شیمیایی در فشارهای بسیار بالا میتوانند با پیچیدگیها و چالشهای زیادی روبرو شوند. در فشارهای بالا، واکنشهای شیمیایی ممکن است باعث تغییرات قابل توجهی در ساختار مولکولها و ترکیبات شیمیایی شود. این تغییرات میتوانند به تخریب ساختارها، تشکیل نمونههای جدید، یا تغییر خواص فیزیکی و شیمیایی منجر شوند. بنابراین، برای انجام واکنشهای شیمیایی در فشارهای بالا، نیاز به مواد و ساختارهای مقاوم و استحکام بالا است.
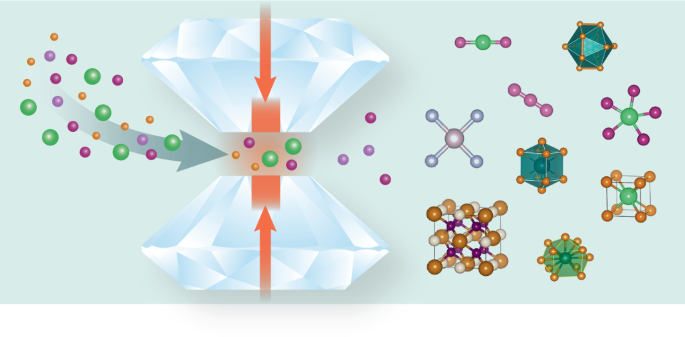
در فشارهای بالا، کنترل دما از اهمیت بالایی برخوردار است. تغییر فشار میتواند تأثیر قابل توجهی بر دما و نرخ واکنشهای شیمیایی داشته باشد. در نتیجه، کنترل دقیق دما و حفظ شرایط حرارتی مناسب برای واکنشها در فشارهای بالا چالشهایی را به وجود میآورد. در برخی از واکنشهای شیمیایی در فشارهای بالا، تطابق مناسب بین سوخت (مواد قابل احتراق) و اکسیدان (مواد تامینکننده اکسیژن) بسیار حائز اهمیت است. عدم تطابق مناسب میتواند منجر به وقوع واکنشهای نامطلوب، افزایش خطر انفجار و کاهش کارایی واکنشها شود.
برای اطلاعات بیشتر مراجعه کنید به این مقاله: Reaction Control
در فشارهای بالا، کنترل فشار و حفظ شرایط فشاری مناسب برای واکنشها بسیار حیاتی است. افزایش فشار میتواند به تغییرات قابل توجهی در سرعت واکنشها، تشکیل فازهای جدید، تغییرات حجم و غیره منجر شود. بنابراین، نیاز به سیستمهای کنترل فشار دقیق و قابل اعتماد در فشارهای بالا وجود دارد.
طراحی، کنترل و بهینهسازی فرایند واکنش
انتخاب و طراحی واکنشگر مناسب، یکی از مهمترین موارد در انجام یک واکنش شیمیایی است. واکنشگر باید شرایط حرارت و فشار مورد نیاز را تامین کند و قابلیت مخلوط شدن مناسب را داشته باشد. همچنین، مقاومت واکنشگر در برابر خوردگی و اثرات شیمیایی نیز باید در نظر گرفته شود. این شامل انتخاب ترکیبات شیمیایی، خلوص مواد اولیه و ویژگیهای فیزیکی و شیمیایی آنها میشود. همچنین، انتخاب مواد با کیفیت مناسب و تأمین منابع مواد اولیه نیز باید در نظر گرفته شود.
مراجعه کنید به این مقاله: Reaction Design & Optimization
کنترل شرایط عملیاتی مانند دما، فشار، pH و غیره در طول واکنش بسیار حیاتی است. این شامل استفاده از تجهیزات کنترل فرآیندی مانند سنسورها، صفحات کنترل، واحدهای خنک کننده است. هدف از کنترل شرایط عملیاتی، دستیابی به یک واکنش یکنواخت و پیشبینیپذیر است. بهینه سازی عملکرد واکنش شامل افزایش بهرهوری واکنش، کاهش ضایعات و فرآیندهای جانبی ناخواسته، بهبود انتخابپذیری محصول و بهبود شرایط ایمنی میشود. بهینهسازی میتواند از طریق تغییر شرایط عملیاتی، فرآیندهای جانبی، طراحی واکنشگر و استفاده از کاتالیستها صورت بگیرد.

کنترل واکنش شامل مانیتورینگ و کنترل پارامترهای وشرایط واکنش مانند دما، فشار، غلظت، سرعت مخلوط کردن و غیره است. این کنترل میتواند به صورت دستی توسط عامل انسانی یا به صورت خودکار با استفاده از سیستمهای کنترل فرآیندی انجام شود. در هر واکنش شیمیایی، ایمنی بسیار حائز اهمیت است. برنامهریزی و اجرای اقدامات ایمنی مناسب برای جلوگیری از وقوع حوادث، کاهش خطرات و محافظت از کارکنان و محیط زیست بسیار حیاتی است. این شامل استفاده از تجهیزات ایمنی، استفاده از مواد ایمن و قابل حمل، طراحی سیستمهای خنککننده مناسب و برنامهریزی آموزشهای ایمنی است.
راکتور مورد نیاز
راکتورها برای انجام واکنشهای شیمیایی در فشارهای بالا استفاده میشوند. راکتورهای استاتیک و دینامیک، راکتورهای با محفظههای فولادی مقاوم در برابر فشار و راکتورهای با حجم قابل تنظیم میتوانند به عنوان تجهیزات اصلی استفاده شوند. راکتورهای قوی و مقاوم برای تحمل فشارهای بالا مورد نیاز است. این راکتورها معمولاً از جنس فولاد ضد زنگ یا آلیاژهای مقاوم در برابر فشار ساخته میشوند. طراحی راکتورها باید از جنبههای ایمنی و کنترل فرایند مربوط به فشارهای بالا در نظر گرفته شود.
برای اطلاعات بیشتر مراجعه کنید به این مقاله: The Role of High-Pressure Reactors in Accelerating Chemical Reactions
راکتورهایی که بتوانند یک واکنش شیمیایی را در فشارهای بسیار بالا مدیریت کنند، باید برخی خصوصیات و ویژگیهای خاص را داشته باشند. راکتور باید از جنسی باشد که توانایی تحمل فشارهای بالا را داشته باشد. فشارهای بالا ممکن است به اندازهای بالا باشند که نیاز به استفاده از فولادهای ضد زنگ یا آلیاژهای خاص مقاوم در برابر فشار داشته باشد.
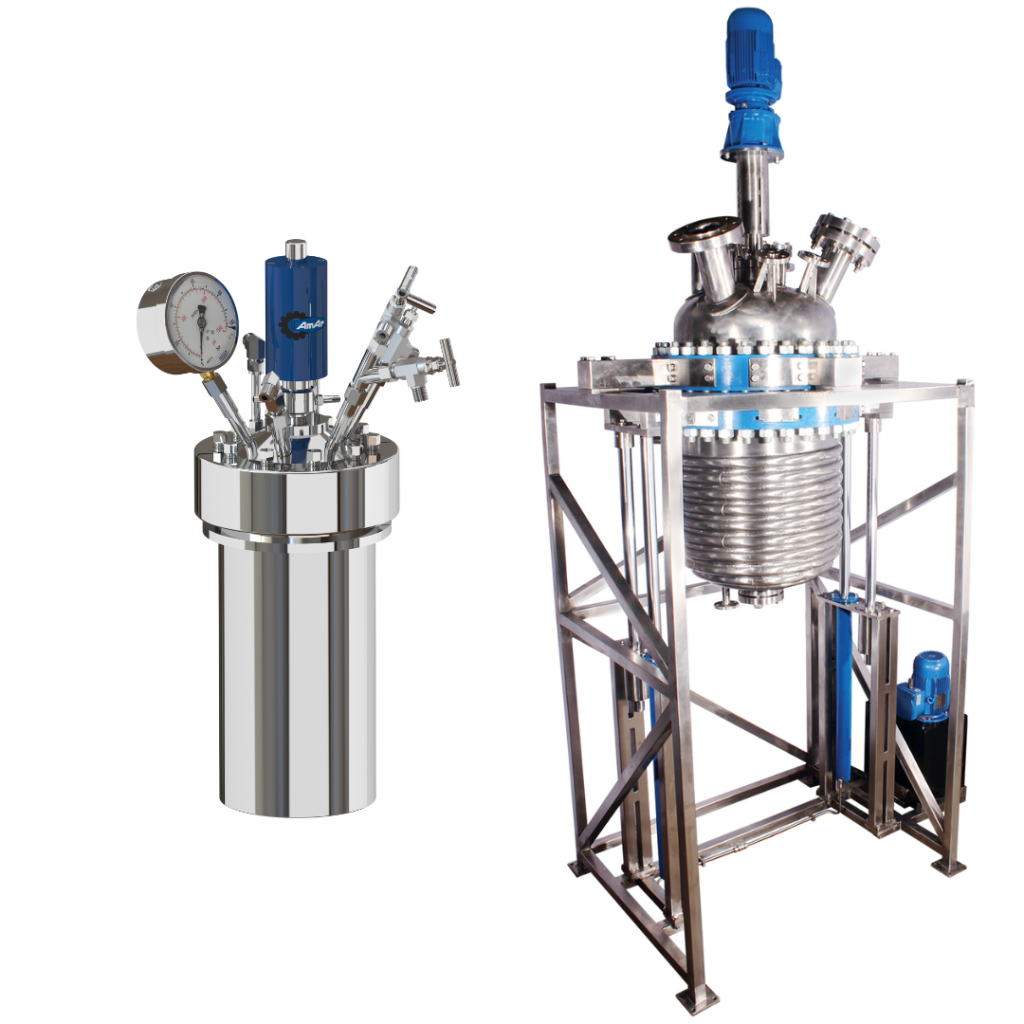
در فشارهای بالا، واکنشهای شیمیایی ممکن است باعث ایجاد شوکها و ضربههای قوی در دیواره راکتور شود. راکتور باید بتواند این شوکها و ضربهها را جذب کند و از خراب شدن و نشت مواد جلوگیری کند. برای واکنشهای شیمیایی در فشارهای بالا، کنترل دقیق دما بسیار حائز اهمیت است. راکتور باید بتواند دمای واکنش را در محدوده مورد نظر نگه دارد و از افزایش یا کاهش ناخواسته دما جلوگیری کند. بنابراین، سیستمهای خنککننده و حرارتی مناسب نیز باید در راکتور موجود باشند.
در فشارهای بالا، کنترل جریان مواد و حجم مخصوص آنها بسیار مهم است. راکتور باید دارای سیستمی باشد که بتواند جریان مواد را بهطور دقیق کنترل کند و از افزایش یا کاهش ناخواسته جریان جلوگیری کند. با توجه به فشار بالا و خطرات مرتبط با واکنشهای شیمیایی، راکتور باید دارای سیستمهای ایمنی مناسب باشد. این سیستمها میتوانند شامل سیستمهای اطلاع رسانی در مورد فشار بیش از حد، دمای بیش از حد، نشت مواد و غیره باشند. همچنین، باید اقدامات ایمنی مرتبط با اطفاء حریق، انتشار گازها و مسائل مرتبط با حفاظت از کارکنان را در نظر بگیرد.
سیستم تأمین فشار در راکتور
برای تأمین فشار در یک راکتوری که واکنش شیمیایی تحت فشار صدها گیگاپاسکال در حال انجام است، نیاز به تجهیزات و سیستمهای قدرتمند و متخصصی است. به علاوه، برای تأمین فشار در اینگونه شرایط، نیاز به استفاده از مواد ساختاری با استحکام بالا مانند فولادهای ویژه، آلمینیومهای تقویت شده و یا کامپوزیتهای مقاوم در برابر فشار است. همچنین، امکان استفاده از سیستمهای خنککننده موثر نیز وجود دارد تا حرارت تولید شده در نتیجه فشار بالا کنترل شود و راکتور در دمای مطلوب عمل کند.
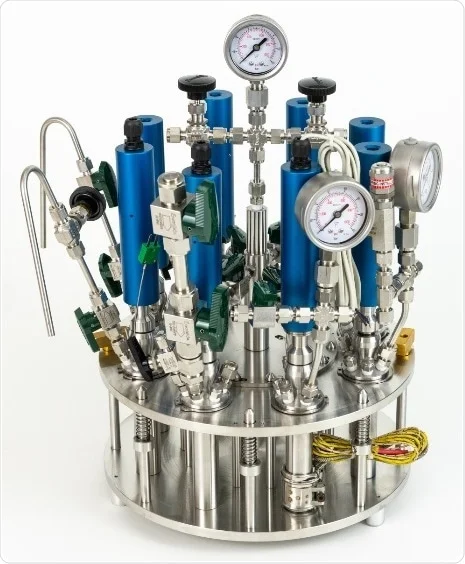
- کمپرسورها از اولین تجهیزاتی هستند که به ذهن میرسند. این دستگاهها برای افزایش فشار گاز یا مایع به فشارهای بالا استفاده میشوند. در صورتی که فشار مورد نیاز بسیار بالا باشد، از کامپرسورهای چند مرحلهای استفاده میشود که باعث افزایش فشار به مقدار مورد نیاز میشوند.
- پمپها نیز در برخی موارد میتوانند برای تأمین فشار استفاده شوند. پمپهایی که برای این منظور استفاده میشوند، معمولاً پمپهای متشکل از چند مرحله هستند که قادر به ایجاد فشارهای بسیار بالا هستند.
- در اکسپنشن جت، از انرژی جنبشی سیال (مثلاً گاز) برای ایجاد فشار استفاده میشود. جتهای اکسپنشن معمولاً در برخی فشارهای بسیار بالا مانند فشارهای گیگاپاسکال استفاده میشوند.
- سیستمهای تشدید فشار میتوانند برای تأمین فشارهای بالا مورد استفاده قرار گیرند. این سیستمها از ترکیبی از پمپها، کامپرسورها، و اجزای مکانیکی و الکتریکی دیگر تشکیل شدهاند که به صورت خاص برای ایجاد فشارهای بسیار بالا طراحی شدهاند.
- راکتورهای هیدرولیکی برای تأمین فشارهای بسیار بالا مورد استفاده قرار میگیرند. این راکتورها از طریق ایجاد شوک هیدرولیکی درون سیال (مانند گاز یا مایع) باعث تولید فشارهای بسیار بالا میشوند.
سیستم میکسر و مخلوطکن
در برخی از فرایندها، مخلوطکردن مواد با فشار بالا اهمیت دارد. میکسر صنعتی شامل تراکمکنندهها، مخلوطکنهای استاتیک و دینامیک و تجهیزات مشابه میشوند. سیستمهای مخلوطکن در راکتورهایی که واکنشهای شیمیایی در فشار بسیار بالا انجام میشوند، نقش مهمی را ایفا میکنند. این سیستمها برای مخلوط کردن مواد و تحریک واکنشهای شیمیایی در داخل راکتور استفاده میشوند. با توجه به فشار بالا و نیاز به انتقال قدر بین الکتروموتور و شفت همزن، یک نوع کوپلینگ مناسب و قابل اعتماد باید مورد استفاده قرار گیرد.
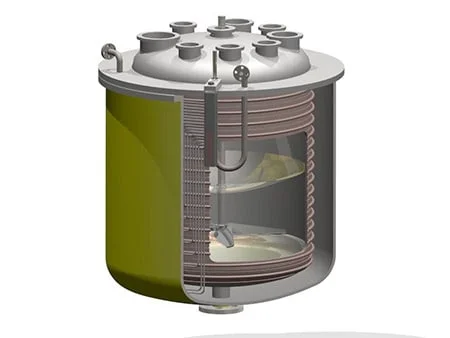
در این حالت، کوپلینگ هیدرولیک به عنوان یک گزینه مناسب میتواند در نظر گرفته شود. کوپلینگهای هیدرولیک از اصول هیدرولیکی برای انتقال قدر استفاده میکنند. آنها شامل دو قسمت اصلی هستند: یک قسمت پیشرانش و یک قسمت دریافت کننده. قسمت پیشرانش معمولاً متصل به الکتروموتور است و قدرت مکانیکی را تولید میکند. قسمت دریافت کننده به شفت همزن متصل میشود و قدرت مکانیکی را به آن منتقل میکند. کوپلینگهای هیدرولیک مزایایی مانند انتقال قدر بالا، عملکرد صاف و بدون لرزش، انتقال نیروی کنترل شده و قابلیت جذب شوکها و ضربهها را دارند. علاوه بر این، آنها معمولاً قابلیت تنظیم زاویه بین الکتروموتور و شفت را نیز دارند.
کوپلینگ مغناطیسی نیز میتواند برای انتقال قدرت در مخازن تحت فشار بین الکتروموتور و شفت همزن در سیستمهای مخلوطکن استفاده شود. کوپلینگ مغناطیسی یک نوع کوپلینگ غیرمستقیم است که بر اساس اصول مغناطیسی عمل میکند.در کوپلینگ مغناطیسی، الکتروموتور و شفت همزن به وسیلهٔ میدان مغناطیسی مشترکی اتصال مییابند. این نوع کوپلینگ بدون استفاده از عناصر مکانیکی مستقیم انتقال قدر را انجام میدهد و در نتیجه لرزش کمتری دارد. همچنین، میدان مغناطیسی قادر است فشارها و لحظههای گشتاور را به طور موثر منتقل کند.
مزایای استفاده از کوپلینگ مغناطیسی شامل عملکرد بیصدا، عدم نیاز به حفظ و تعمیر قطعات مکانیکی، انتقال قدر بالا و نیروی کنترل شده، و عدم نیاز به روانکاری و گریس کردن مجدد کوپلینگ است. همچنین، کوپلینگ مغناطیسی میتواند در محیطهای خاصی مانند محیطهای شیمیایی آلوده، با دما و فشار بالا و حتی در محیطهای خطرناک استفاده شود.
سیستمهای کنترل و اندازهگیری
برای کنترل دقیق فرایندها و اندازهگیری پارامترهای مرتبط با واکنشهای شیمیایی، نیاز به سیستمهای کنترل و اندازهگیری مناسب است. این سیستمها شامل سنسورها، شاخصها، کنترلکنندهها، دماسنجها، فشارسنجها و سایر تجهیزات مرتبط میشوند. برای کنترل دقیق فرایندهای شیمیایی در فشارهای بالا، نیاز به سیستمهای کنترل و اتوماسیون پیشرفته است. این سیستمها شامل سنسورها، کنترلکنندهها، صفحات نمایش، سیستمهای ضبط داده و نرمافزارهای مرتبط با کنترل فرایند میشوند.
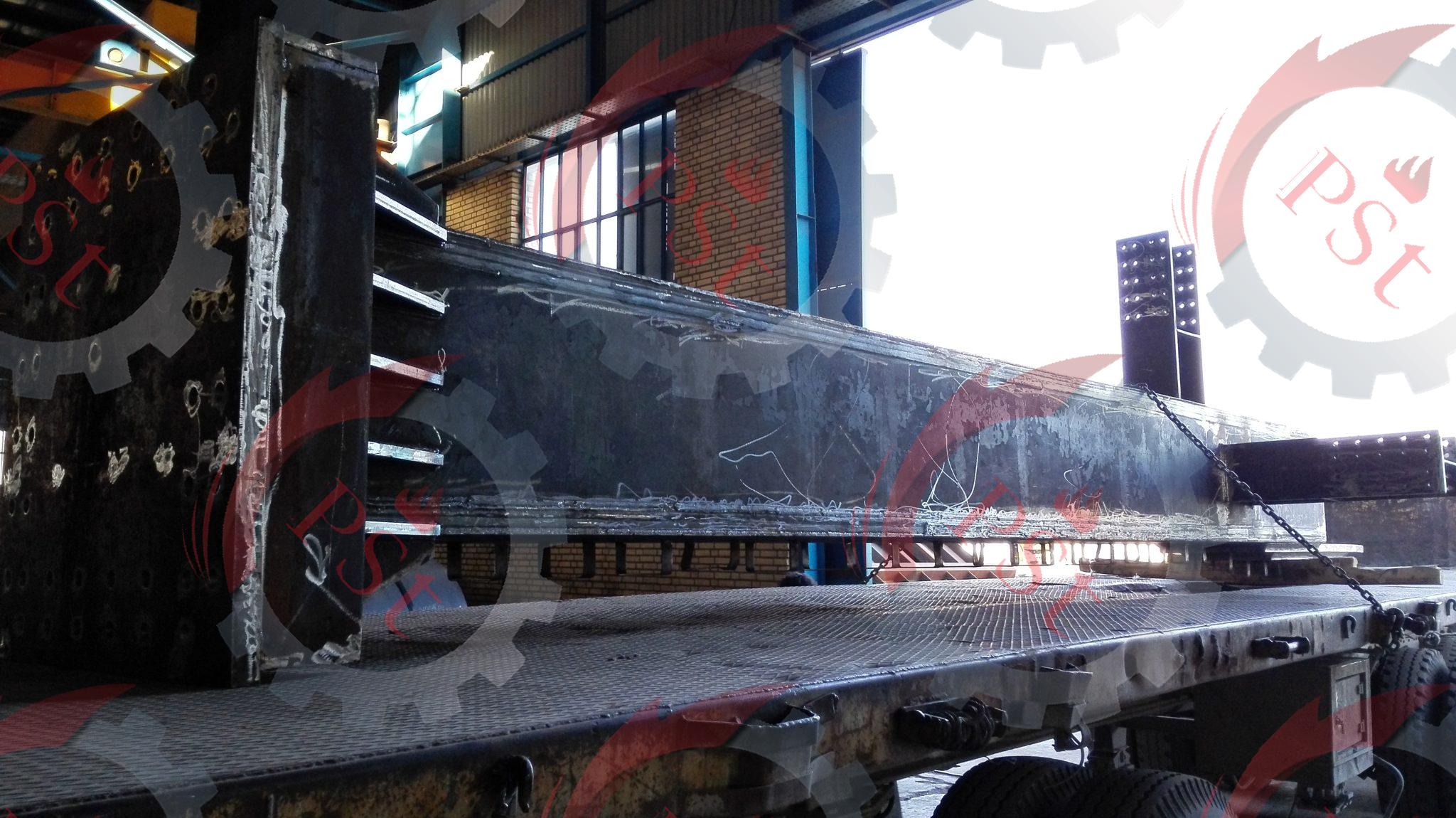
سنسورها در سیستمهای کنترل و اندازهگیری نقش اساسی دارند. سنسورها برای اندازهگیری و مانیتورینگ پارامترهای مختلف مانند فشار، دما، جریان، سطح و غیره استفاده میشوند. در فشارهای بالا، سنسورهایی با قابلیت تحمل فشار بالا و دقت بالا باید مورد استفاده قرار گیرند. سنسورهای فشار مممکن است با استفاده از تکنولوژیهایی مانند سنسورهای فشار فشار بالا (High-Pressure Pressure Sensors) یا سنسورهای پیزوالکتریک (Piezoelectric Sensors) طراحی شوند.
ترانسمیترها به عنوان واسطهای بین سنسورها و سیستم کنترل استفاده میشوند. آنها اطلاعات از سنسورها را تبدیل و تقویت کرده و به فرمت مناسب برای ارسال به کنترلر مرکزی تبدیل میکنند. ترانسمیترهایی با قابلیت تحمل فشار بالا و مقاوم در برابر شرایط سخت مانند فشار، دما و ویبراسیون معمولاً در این بستر استفاده میشوند.
کنترلر مرکزی، سیستمی است که وظیفه کنترل و مدیریت عملکرد سیستم را بر عهده دارد. این کنترلر با دریافت اطلاعات از سنسورها و ترانسمیترها، عملکرد سیستم را تحلیل کرده و تصمیمات لازم را بر اساس شرایط و روند واکنش اتخاذ میکند. کنترلر مرکزی میتواند از روشهای کنترل پیشرفته مانند کنترل PID (Proportional-Integral-Derivative) استفاده کند تا به طور دقیق تر و بهینهتر کنترل خود را انجام دهد.
در فشارهای بالا، تجهیزات و سیستمهای کنترل و اندازهگیری باید از نظر محافظت و عایقبندی مناسب باشند. عوامل مانند فشار، دما، ترکیبات شیمیایی و غیره میتوانند بر تجهیزات تأثیر منفی بگذارند. بنابراین، استفاده از محافظتهای مناسب مانند محافظت فیزیکی (مانند قطعات فلزی محافظ)، عایقبندی مقاوم در برابر شرایط سخت و استفاده از مواد مقاوم در برابر خوردگی و فشار بالا میتواند از کارکرد صحیح و دقیق تر تجهیزات تضمین کند.
سیستم خنک کننده و انتقال حرارت
سیستم خنککننده کاربید سیلیسیم یک راه حل پیشرفته در حوزه خنککنندههای صنعتی است که به طور خاص در برخی از راکتورهای شیمیایی استفاده میشود. در این سیستم، از کاربید سیلیسیم به عنوان ماده خنککننده استفاده میشود که دارای ویژگیهای منحصر به فردی است که آن را برای کاربردهای حرارتی مناسب میکند. کاربید سیلیسیم یک ماده سرامیکی است که متشکل از کاربید سیلیسیم (SiC) است. این ماده به دلیل ویژگیهایی نظیر مقاومت در برابر حرارت بالا، مقاومت مکانیکی بالا، مقاومت در برابر خوردگی و خواص حرارتی خوب، به عنوان یک ماده خنککننده مناسب در راکتورهای شیمیایی مورد استفاده قرار میگیرد.
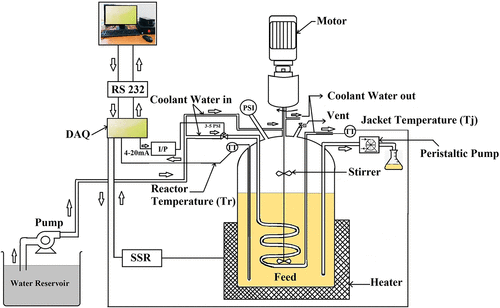
فشارهای به این مقدار بسیار بزرگ هستند و نیازمند طراحی و ساخت مواد و تجهیزات ویژهای هستند. برای خنک کردن راکتورهای با فشار بالا معمولاً از سیستمهای خنککننده آب با فشار بالا استفاده میشود. در این سیستمها، استفاده از مواد مقاوم به فشار مانند فولادهای ضدزنگ، نیکل و آلیاژهای مقاوم در برابر فشار مانند آلیاژهای آلومینیوم-برونز از جمله روشهای استفاده شده است. همچنین، کیفیت ساخت و مهندسی برای طراحی سیستم خنککننده در فشارهای بالا بسیار حائز اهمیت است.
در مواردی که نیاز به تحمل فشارهای بسیار بالا مانند صدها گیگاپاسکال وجود دارد، راهکارهای خاصی مانند استفاده از مواد جدید با خواص مکانیکی استثنایی مورد استفاده قرار میگیرد. به عنوان مثال، برخی از مواد خنککننده نوین مانند کریستال هلیکالی و گرافن با توانایی تحمل فشارهای بالا در حوزه نانوفناوری مورد مطالعه و توسعه قرار میگیرند. با این حال، باید توجه داشت که استفاده از اینگونه مواد و تکنولوژیها هنوز در مراحل پژوهشی و تجربی قرار دارد و اجرای عملیاتی آنها در مقیاس بزرگ ممکن است هنوز به چالشهای فنی و عملیاتی برخورد کند.
سیستم ایمنی
سیستم ایمنی در یک راکتور سنتز شیمیایی که در آن واکنشی تحت فشار صدها گیگاپاسکال در حال انجام است، بسیار حیاتی و اساسی است. این سیستمها به منظور حفظ ایمنی عملیات و جلوگیری از وقوع حوادث و شرایط خطرناک طراحی و اجرا میشوند. در فشارهای بالا، ایمنی و احتیاط بسیار مهم است. تجهیزات ایمنی شامل شیرها و والفها، سیستمهای خاموش کننده حریق، دستگاههای ایمنی شخصی (مانند کاپسولهای نجات) و سایر تجهیزات ایمنی برای حفاظت از کارکنان و محیط میشوند.
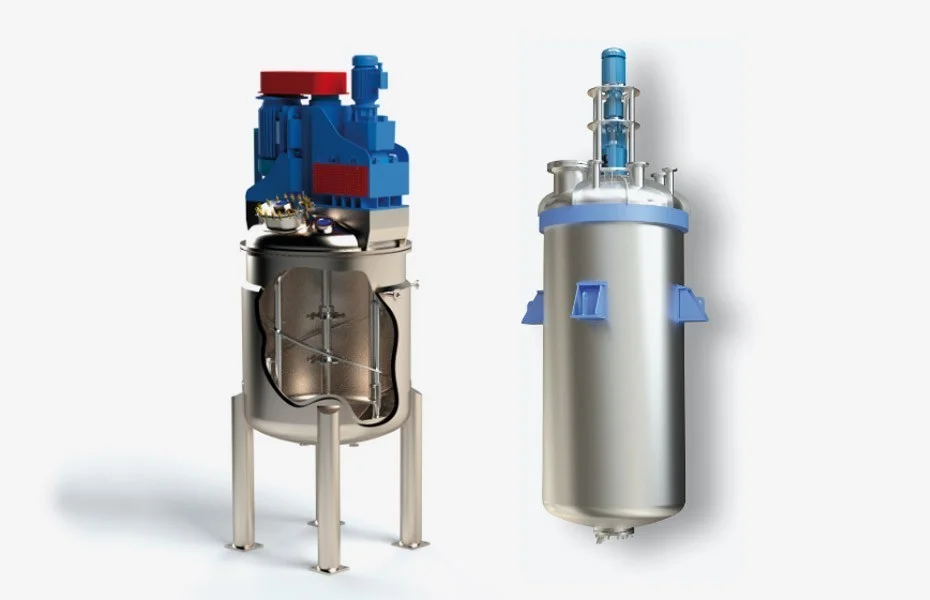
در ابتدای فرآیند طراحی راکتور سنتز شیمیایی، ایمنی باید به عنوان یک اصل اساسی در نظر گرفته شود. این شامل طراحی ساختار فیزیکی راکتور، انتخاب مواد ساختاری مقاوم در برابر فشار و دما، و ایجاد سیستمهای ایمنی فشار بالا برای کنترل و مدیریت فشار در دستگاه میشود. در راکتورهای با تحمل فشار صدها گیگاپاسکال، سیستمهای کنترل فشار بسیار حساس و حیاتی هستند.
این سیستمها شامل سنسورهای فشار دقیق، تجهیزات کنترل فشار هستند. هدف اصلی این سیستمها، حفظ فشار در محدوده ایمن و جلوگیری از افزایش غیرقابل کنترل فشار در راکتور است. با توجه به واکنشهای سنتز شیمیایی با فشار بالا، سیستم خنککننده بسیار مهم است. این سیستم به منظور حفظ دمای مطلوب در دستگاه و جلوگیری از افزایش دما به مرزهای خطرناک طراحی میشود.