کورههای حرارتی صنعتی، دستگاههایی هستند که برای ایجاد حرارت بالا و کنترل شده در فرآیندهای صنعتی استفاده میشوند. این کورهها معمولاً برای گرمکردن و ذوب مواد مختلف، تصفیه و پخت مواد غذایی، تولید فولاد و فلزات، سرامیک، شیشه، سیمان و بسیاری از صنایع دیگر مورد استفاده قرار میگیرند. کورههای حرارتی صنعتی میتوانند با استفاده از منابع انرژی مختلفی مانند گاز طبیعی، نفت، ذغال سنگ، برق، ناخالصیهای صنعتی و حتی اشعه الکترومغناطیسی ایجاد شوند. طراحی و عملکرد این کورهها بستگی به نوع فرآیند و مواد مورد استفاده دارد.
کورههای حرارتی صنعتی مثل اتوکلاو پخت سیلیکات معمولاً دارای یک فضای داخلی بزرگ و عایقهای حرارتی هستند تا حرارت تولید شده در داخل کوره را درون حفره نگه دارند. آنها میتوانند دارای سیستمهای کنترل حرارتی پیشرفته باشند که دمای کوره را در محدوده مورد نظر نگه میدارند و از بیشبودن یا کمبودن حرارت جلوگیری میکنند.
نوع کوره | طرز کار |
کورههای القایی | از اصل القای فولاد مایع برای گرمکردن و ذوب فلزات استفاده میکنند |
کورههای قوس الکتریکی | برای ذوب فلزات با استفاده از قوس الکتریکی بین الکترودها استفاده میشوند |
کورههای برقی مقاومتی | از جریان برقی عبوری از مواد مقاوم برای تولید حرارت استفاده میکنند |
کورههای گازی | با استفاده از احتراق گازها مانند گاز طبیعی یا پروپان حرارت تولید میکنند |
کورههای ذغال سنگ | از ذغال سنگ به عنوان سوخت استفاده میکنند تا حرارت لازم را تولید کنند |
هر نوع کوره صنعتی، بسته به نیاز و متغیرهای فرآیندی، مزایا و محدودیتهای خاص خود را دارد. مزیتهای استفاده از کورههای حرارتی صنعتی عبارتند از:
- قابلیت تولید حرارت با دماهای بالا و کنترل دقیق آن، که برای فرآیندهای صنعتی حساس به دما بسیار مهم است.
- قابلیت تولید حجم بزرگی از حرارت در یک زمان، که برای فرآیندهایی که نیاز به ذوب و گرمکردن مواد بزرگ دارند، مناسب است.
- انعطافپذیری در استفاده از منابع انرژی مختلف، مانند گاز طبیعی، ذغال سنگ، نفت و برق.
- قابلیت تطبیق با نیازهای مختلف صنایع و فرآیندهای مختلف، مانند تولید فولاد، شیشه، سرامیک و غیره.
کوره های صنعتی فولادی
کورههای صنعتی که با فولاد ساخته میشوند، به عنوان کورههای فولادی شناخته میشوند. این نوع کورهها برای تولید، ذوب و فرآوری فولاد و سایر فلزات آهنی استفاده میشوند. طراحی و ساخت این کورهها برای تحمل دماهای بسیار بالا، مقاومت در برابر خوردگی و شرایط سخت صنعتی به کار میرود. کورههای صنعتی فولادی معمولاً از مواد مقاوم در برابر حرارت و فشار بالا تشکیل شدهاند.
بدنه کوره فولادی معمولاً از ورقهای فولادی ضخیم ساخته میشود که تحمل دماهای بالا را دارند. برای افزایش مقاومت در برابر حرارت، در برخی از موارد از مواد سرامیکی نیز استفاده میشود. برای کاهش انتقال حرارت از کوره به محیط خارجی و حفظ دمای داخلی، عایق حرارتی استفاده میشود. معمولاً از مواد مقاوم در برابر حرارت مانند بنتونیت، سیلیکات کلسیم و سیلیکات آلومینیوم برای ایجاد عایق استفاده میشود.
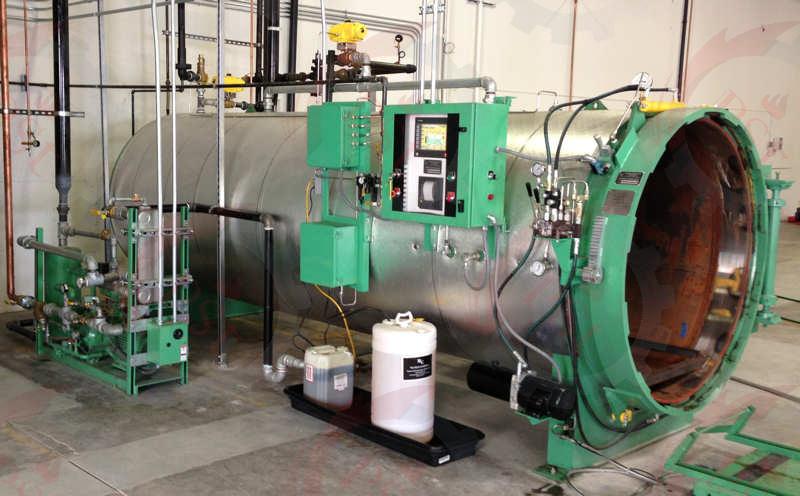
روکش داخلی کوره معمولاً از مواد مقاوم در برابر حرارت و خوردگی مانند آجرهای آتشساز، آجرهای سیلیکا، رفراکتورها و یا آجرهای آلومینا ساخته میشود. این روکش به منظور مقاومت در برابر اثرات حرارتی و شیمیایی فرآیند، در داخل کوره قرار میگیرد. سیستم حرارتی شامل سوختدهنده و سیستم انتقال حرارت میشود. در کورههای فولادی، سوختدهنده معمولاً شامل بخار آب، گاز طبیعی، نفت یا ذغال سنگ است. سیستم انتقال حرارت میتواند شامل سیستمهای هوایی، آبی یا انتقال حرارت ترکیبی باشد، که بسته به نوع کوره و نیازهای فرآیند متفاوت است.
در کورههای صنعتی فولادی مثل کوره اتوکلاو، سیستم کنترل برای کنترل دما، فشار و سایر پارامترهای مرتبط با فرآیند استفاده میشود. این سیستم معمولاً شامل حسگرها، کنترلرها و دستگاههای اجرایی مانند شیرها و والوها است. این سیستم کنترل به وسیله مهندسان و عملیاتکنندگان مورد استفاده قرار میگیرد تا فرآیند را به طور دقیق کنترل و نظارت کنند.
حداکثر دما در کوره های صنعتی
کورههای صنعتی فولادی قابلیت تحمل دماهای بسیار بالا را دارند. دمای عملیاتی کورههای صنعتی فولادی معمولاً بین 1000 درجه سانتیگراد (1832 درجه فارنهایت) تا 2000 درجه سانتیگراد (3632 درجه فارنهایت) قرار دارد. این دماها بسته به نوع فرآیند، نوع فولاد و نیازهای تولید متغیر است. برای مثال، در فرآیند ذوب فولاد، کورههای صنعتی ممکن است به دماهای فوق العاده بالا، حدود 1500-1800 درجه سانتیگراد (2732-3272 درجه فارنهایت) برسند. این دماها برای ذوب فولاد و تبدیل آن به حالت مایع استفاده میشود.
در عملیاتهای دیگر نیز، مانند تصفیه، تصلیب و تصفیه نهایی فولاد، کورههای صنعتی ممکن است به دماهای مختلف دست یابند. به طور کلی، آهن و فولاد در دماهای بالا انعطاف و قابلیت تغییر شکل بیشتری دارند و میتوانند فرآیندهای مختلفی را در دماهای متفاوت تحمل کنند. برای کورههای صنعتی فولادی این که بتوانند دمای مورد نیاز فرآیندهای فولادسازی را حفظ کنند و در عین حال از مقاومت و استحکام کافی برخوردار باشند تا با شرایط سخت صنعتی و فشارهای حاکم در داخل کوره سازگار باشند بسیار با اهمیت می باشد.
برای تحمل دماهای بسیار بالا در کورههای صنعتی فولادی، از آلیاژهای خاصی استفاده میشود که دارای مقاومت حرارتی بالا باشند. این آلیاژها معمولاً شامل فولادهای ضدزنگ مبتنی بر نیکل و کروم، فولادهای ضدزنگ مارتنزیتی، و فولادهای ضدزنگ سوپرآلیاژها میشوند.
آلیاژ | خصوصیات |
فولاد ضدزنگ استنلس استیل | این نوع فولاد ضدزنگ حاوی نیکل و کروم است و دارای مقاومت بالا در برابر خوردگی و حرارت است. فولاد استنلس استیل معمولاً در دماهای بالا تا حدود 1200 درجه سانتیگراد (2192 درجه فارنهایت) کاربرد دارد. |
فولادهای مارتنزیتی | این نوع فولادها دارای محتوای کروم بالا هستند و مقاومت حرارتی مناسبی دارند. آلیاژهای معروف مارتنزیتی شامل فولادهای 9Cr-1Mo و 9Cr-1Mo-V هستند که به طور معمول در دماهای بین 500 تا 600 درجه سانتیگراد (932 تا 1112 درجه فارنهایت) استفاده میشوند. |
سوپرآلیاژها | این آلیاژها شامل ترکیباتی از نیکل، کروم و عناصر دیگر مانند مولیبدن، تنگستن و کبالت هستند. سوپرآلیاژها دارای مقاومت بسیار بالا در برابر حرارت، خوردگی و فشار هستند. آلیاژهای معروف سوپرآلیاژها شامل Inconel، Hastelloy و Haynes میباشند. این سوپرآلیاژها به طور معمول در دماهای بالای 1000 درجه سانتیگراد (1832 درجه فارنهایت) استفاده میشوند. |
طراحی و ساخت کوره صنعتی
طراحی و ساخت کوره حرارتی صنعتی به معنای طراحی و ساخت یک ساختار فیزیکی و مکانیکی است که بتواند دماهای بالا را تولید و حفظ کند. کورههای حرارتی صنعتی معمولاً برای عملیات گرمایش، ذوب، تصفیه و فرآیندهای دیگری که نیاز به دماهای بسیار بالا دارند، استفاده میشوند. انتخاب مواد ساختاری برای کوره بسیار مهم است. این مواد باید قابلیت تحمل دماهای بالا، مقاومت در برابر خوردگی، فشار و سایر شرایط سخت صنعتی را داشته باشند. مواد معمولاً شامل فولادهای خاص، آلیاژهای مقاوم در برابر حرارت و سوپرآلیاژها هستند.
طراحی ساختار و ابعاد کوره نیز بر اساس نیازهای فرآیند و دمای مورد نیاز صورت میگیرد. این شامل اندازهگیری و تعیین ابعاد مناسب برای دستگاه، طول و عرض کوره، ضخامت دیوارهها و سایر جزئیات ساختاری است. یک کوره حرارتی صنعتی نیاز به سیستم حرارتی مناسب دارد که بتواند دماهای مورد نیاز را تولید و حفظ کند. این شامل سیستم سوخترسانی، سیستم احتراق، سیستم هوادهی و تهویه، سیستم خنککننده و سایر اجزای مرتبط است. در ساختار و کنترل کوره حرارتی، از تکنولوژیهای پیشرفته مختلف استفاده میشود. در زیر، به برخی از این تکنولوژیها اشاره میکنیم:
- استفاده از سیستمهای کنترل خودکار، از جمله کنترلرها، سنسورها و الگوریتمهای پیشرفته، به کنترل دقیق و هوشمندانهتر کوره حرارتی کمک میکند. این سیستمها با اندازهگیری پارامترهای مختلف مانند دما، فشار و جریان، به صورت خودکار تنظیمات لازم را برای دستیابی به شرایط عملیاتی مطلوب انجام میدهند.
- سنسورها برای اندازهگیری دقیق پارامترهای حرارتی و عملکرد کوره استفاده میشوند. این شامل سنسورهای دما، فشار، رطوبت و جریان است. همچنین، با استفاده از شبکههای حسگری، امکان مانیتورینگ و کنترل بیشتر از راه دور نیز فراهم میشود.
- با استفاده از شبکههای ارتباطی و اینترنت اشیا، کورههای حرارتی میتوانند به صورت متصل به شبکههای دیگر و سیستمهای مدیریتی بزرگتر باشند. این امکان را فراهم میکند تا اطلاعات مربوط به عملکرد کوره، مانیتورینگ و کنترل از راه دور انجام شود.
- تکنولوژیهای هوشمند مانند هوش مصنوعی و یادگیری ماشینی میتوانند در بهینهسازی عملکرد کوره و کاهش هدررفت انرژی کمک کنند. با استفاده از الگوریتمهای هوشمند، میتوان بهبود عملکرد کوره، کاهش زمان و هزینههای عملیاتی و افزایش بهرهوری را دست یافت.
- با استفاده از رایانش ابری، امکان ذخیره و پردازش حجم بزرگی از دادههای مربوط به کوره حرارتی و نیز به اشتراک گذاری اطلاعات با سایر سیستمها و کاربران فراهم میشود. این امکان به مدیران کمک میکند تا دادهها را به صورت مرکزی مدیریت کنند و تحلیلهای پیشرفتهتری را بر روی آنها انجام دهند.